Explore our extensive product range below.
Stauff Tube Clamps
Product Information of Stauff Clamps
6. Installations:
STAUFF Clamps offer fast, easy, and secure installation of pipes, tubes, hoses, cables, and other flexible and stiff components with outer diameters up to 1016 mm / 40.00 inch. Hence, this feature allows Stauff clamps to be readily disassembled.
There are several types of weld base plates built in accordance with DIN 3015 that may be installed in a variety of customized special clamp designs. Please refer to the following three installation procedures based on the work requirements:
i. Installation Option 1: Base plate installation
The most common fundamental use is base plate installation. The base plate is used to mount to the wall or ceiling, and the clamps may be simply inserted before final tightening with the cover plate and bolts and screws.
To tighten the entire set of clamps, two typical thread types are used: Metric thread (M) and UNC thread (U).
- Step 1: Placing the base plate in the indicated places, making sure that the placements are appropriate for the system’s projected loads.
- Step 2: Marking the base plate positions to assure the best system alignment.
- Step 3: Welding the base plate into place. Alternatively, an extended base plate can be mounted to their positions using two screws or bolts at both ends without any welding job.
- Step 4: Pressing the clamp’s one halves onto the base plate’s bottom.
- Step 5: Connecting the pipe, tube, wire, hose, or other line.
- Step 6: Placing the second halves of the Stauff clamp and covering plate on top. Mount the full clamp installation with bolts and screws.
During the clamp assembly, the bolts length relates to the installation of the base plate and mounting rails, as well as the stacking level.
ii. Installation Option 2: Installation on mounting rail
In order to arrange multiple sets of clamps along the pipe or tube, mounting rails are utilized during installation. The clamps can be readily adjusted before final tightening using mounting rails, and additional sets of clamps can be added or withdrawn without difficulty. Rail nuts have been designed to optimize and adapt the shape. Both ends of the bottom portion were gently chamfered, and the rail nuts could be screwed in further to increase the contact surface area with the mounting rail. Before being firmly attached, the rail nut actual locations of the clamp assemblies can be changed.
- Step 1: Positioning the mounting rail in the designated location, taking into account the anticipated loads.
- Step 2: Labelling the mounting rail positions to assure the best system alignment.
- Step 3: Welding the mounting rails into place, or use side-mounting brackets with bolts or screws to mount it.
- Step 4: Inserting rail nuts into the mounting rail and changing the position until they are locked at the mounting rail for standard and twin series, whereas rail nuts for heavy series have been fitted by sliding in from the mounting rail’s end.
- Step 5: Placing one halves of the clamp body on the rail nuts.
- Step 6: Inserting the pipe, tube, cable, hose, or other line.
- Step 7: Mounting the whole clamp installation with bolts and screws by placing the second parts of the clamp and cover plate on top.
iii. Installation Option 3:
Multiple clamp bodies of the same size can be mounted directly on top of one another with the use of safety locking plates and stacking bolts in clamp installation. Stacking clamps allow installers to be more flexible in the design and placement of pipeline systems. This is due to the fact that numerous lines running closely together no longer have to be placed side by side. To prevent stacking bolts from turning around, safety locking plates are inserted between clamp levels. Stacking clamps can be installed on either mounting rails or a base plate.
- Step 1: Assembling the bottom clamp halves to the base plate or rails nuts.
- Step 2: Connecting the pipe, tube, cable, hose, or other line.
- Step 3: Installing the clamp’s second halves.
- Step 4: During assembly, insert one stacking bolt into each single bolt hole on the clamp and tighten using the tightening torques.
- Step 5: Placing the safety locking plate on top of the clamp body assembly’s first level.
- Step 6: Moving on to the next level. When you reach the upper level of the clamp assembly, insert the cover plate and hexagon head bolts. Tighten the bolts using the tightening torques table as a guideline.
Download:
Pipe Clamps
Types of Clamps
ADJUSTMENT: This hanger provides for a vertical adjustment of 1 to 2 inches with the pipe and hanger in position. A temporary support is not required while adjustment is being made.
FINISH: Hangers can be furnished galvanized. Specify when ordering.
ORDERING: Specify figure number, pipe size and description.
MATERIAL: Yoke, load bolt and load distribution strap is chrome molybdenum steel. U-Bolt is stainless steel.
SERVICE: Recommended for suspension of high temperature piping requiring 4 to 6 inches of insulation.
MAX. TEMP: 1100°F
ORDERING: Specify figure number, pipe size and description.
MATERIAL: Yoke, load bolt and load distribution strap is chrome molybdenum steel. U-Bolt is stain-less steel.
SERVICE: Recommended for suspension of high temperature piping requiring 4 to 6 inches of insulation.
MAX. TEMP: 1100°F
ORDERING: Specify figure number, nominal pipe size, and description.
SIZE RANGE: 1/2 inch thru 36 inches
MATERIAL: Carbon steel
FINISH: Black or galvanized; furnished black unless otherwise specified.
SERVICE: Recommended for suspension of cold pipe lines or hot lines where little or no insulation is required.
MAX. TEMP.: 750°F
ORDERING: Specify figure number, pipe size, description and finish.
SIZE RANGE: 3 inches thru 36 inches
MATERIAL: Carbon steel
FINISH: Black or galvanized; furnished black unless otherwise specified.
SERVICE: Recommended for suspension of cold or hot pipe lines with heavy load having little or no insulation.
MAX. TEMP.: 750°F
ORDERING: Specify figure number, pipe size, description and finish.
SIZE RANGE: 1/2 inch thru 36 inches
MATERIAL: Carbon steel
FINISH: Black or galvanized; furnished black unless otherwise specified.
SERVICE: Recommended for suspension of cold or hot pipe lines requiring little insulation or insulation up to 4 inches
MAX. TEMP.: 750°F
ORDERING: Specify figure number, pipe size, description and finish.
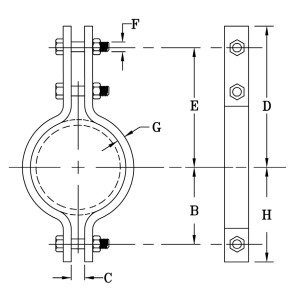
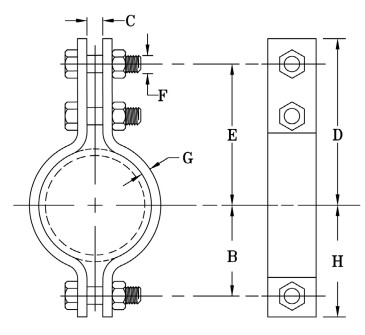
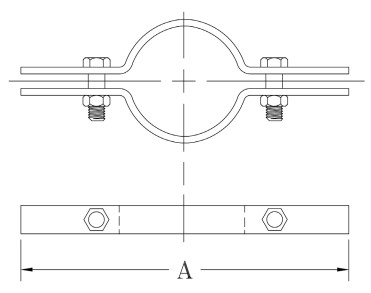
SERVICE:
In situations where the use of a welded lug attachment would create an undesirable crushing effect on the pipe wall, this clamp can transfer the load from the pipe wall to the riser clamp by means of hold-down lugs welded to the pipe.
Clamps may be furnished in either Carbon or Alloy steel with bolting to suit, using an allowable stress of 10,000 PSI. Temperature correction factors listed in “CHART A” are based on allowable stresses listed in MSS-SP-58.
METHODS OF SELECTION:
1. Determine total load to be supported and service temperature of the piping system.
2. Refer to “CHART A (table below)” and determine the temperature correction factor for the clamp material being used.
3. Multiply total load by the correction factor to obtain a corrected load.
4. Refer to “CHART C (below)” and locate the point determined by the intersection of the total load co-ordinate and the pipe size curve. Project this point horizontally until it intersects with the “D” dimension coordinate. Directly above this point is the required stock size.
5. The bolt diameter is obtained by using the uncorrected total load and referring to “CHART B (below)”.
ORDERING: Specify pipe outside diameter, total load, design temperature, material and dimension “D” or center to center of hanger rods.
NOTE: Pipe clamp can be fabricated to any specified material.
Contact Us Today
Your Leading Stockist of Pipe, Tubes, Fittings, Flanges and Specialist Forgings in Duplex, Chrome Alloy and Nickel Alloys